Ultrasonic Immersion Scanners For NDT
Four Axis Manipulator For Ultrasonic Immersion Scanning System For Aluminum Shafts And Flats |
The Ultrasonic Immersion Scanning System is used for detecting flaws in Aluminum Alloy Rods & Flats, Submerged in water in stainless steel tank.
The rod test piece sizes vary from 30 mm to 240 mm dia. & are 400 to 4000 mm long. The flats are 400 to 4000 mm long, 100 mm to 650 mm wide & 15 mm to 150 mm thick.
The Ultrasonic Scanner Probe is mounted on Z Axis & with the PC Based Controller & Stepper Drives Various X Step Y, Y Step X, R Step X, & X Step R Movements are achieved.
The encoders are put on each X, Y, and R axis for feedback & precise control movement. Four nos. Stainless Steel Jacks with Delrin Nut have been provided in the SS Tank to facilitate lifting & lowering of flats weighing up to 1200 kgs.
Four Axis Manipulator For Ultrasonic Scanning Of SS Forging |
- The UT Scanner is used for detecting flaws in end fittings Rotational Indexing Movement to 190 mm dia., 2550 mm long Test Piece, along with calibration piece.
- Ball Lead Screw Driven X (3300 mm), Y (400 mm), Z (150 mm) tables with linear guides for probe movement
- PC Based Stepper Motor Controls.
- Capable of Picking up Echo from 1.2 mm dia. Flat Bottom Hole.
- Oil Circulating System.
XYZ Scanner for UT Scanning |
- Under water in a See-Through Acrylic Tank and the Probe is moved in user-defined path over the job.
- The Control System consists of a Personal Computer with 4-Axis motion control card mounted inside a PCI slot of the PC. The same PC is also used to log the Ultrasonic Data.
- Stepper motors & Micro-stepping drives are used for all the three axes.
6-Axis Immersion Scanner for Ultrasonic Testing of Contoured Objects |
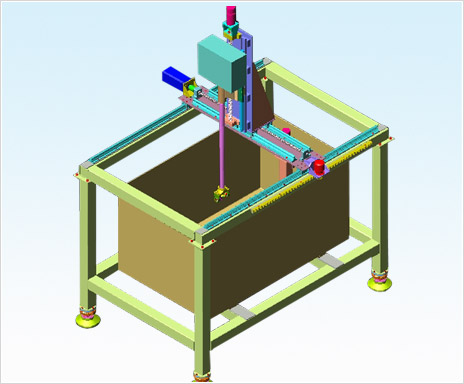
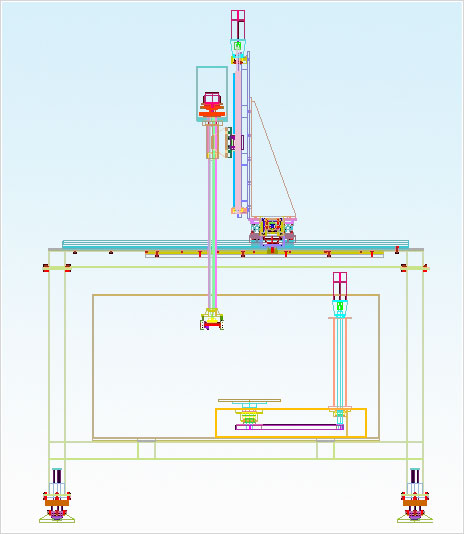
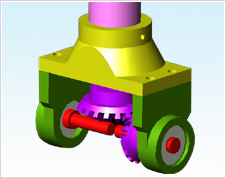 |
The scanner is used to carry out Ultrasonic Immersion testing of contoured objects. The scanning is done inside a 1.2m x 0.7m x 0.6m S.S. tank. The scanning is done by providing the following movements to the probe:
|
- Stepper motor driven Y-Axis movement for moving the test bridge along the width of immersion tank
- Stepper motor driven Z-Axis movement for moving the test bridge along the depth of immersion tank
- Stepper motor driven 360º Swivel & ± 90º Gimbel movements for moving the probe over the job.
The motion to the job is provided by a Rotary Turn Table, locatable in the center of the tank as and when required, capable of continuous rotation with an object weight of 50 kgs.
Stepper Motor Driven Z-θ Scanner |
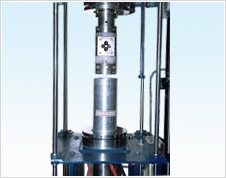 |
The PC controlled scanner is designed for inspection of stationary test pipe from ID side by providing linear and rotary motion to inspection head, under immersed condition. |
Linear Movement :
Stroke |
: |
750mm |
Speed |
: |
1-25 mm/s |
Accuracy |
: |
0.3 mm |
Repeatability |
: |
0.1 mm |
|
Rotational Movement :
Movement |
: |
0 - 360° |
Speed |
: |
1-50 rpm. |
Accuracy |
: |
0.3° |
Repeatability |
: |
0.1° |
|
UT inspection head for Tubes/ Pipes
To access the integrity of objects such as tubes / pipes, UT method has been well accepted. For QA/QC of such parts codes such as ASTM, ASME, and IAEA etc. are already established. For inspecting tubes / pipes, a multi-probe based UT method can drastically reduce the inspection time. To cater to such needs, a "Multi Sensor Inspection Head" has been developed. This approach enables the UT expert to conveniently detect circumferential and axial defects and also perform dimensional measurement with help of controlled movement of the head from ID side in an immersion-scanning mode.
UT Scanner for Tube To Tube Sheet Weld Inspection of Heat Exchanger |
Two Axis Manipulator for Online UT Scanning of M.S. Plates |
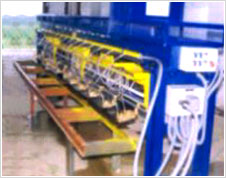 |
The system is designed for scanning 1100 mm to 4700 mm wide MS Plates, having thickness of 6 to 65 mm. The Plates are moving on a conveyor having Maximum Speed of 3 m/min.
There are total 14 Probe Holders (For Holding Ultrasonic Probes) out of which 4 are fixed for edge sensing and balance 10 are continuously horizontally reciprocated for stroke length of 460 mm at a speed of 14m/min.
|
This testing is carried out before these plates are converted into Saw Pipes.
The horizontal reciprocating system comprises of ball lead screw with linear guides driven by servomotor and drive. The speed can be varied from 1.5 m/min. to 15 m/min. The reciprocating arm has two guided rods on which probe holders are mounted. This entire reciprocating system can be lifted or lowered automatically with the help of sensors to sense presence or absence of plates. The specially designed probe holders have water inlets and water flows through each of them through a common manifold.
The four fixed probes at two ends can be slided and fixed at desired locations in event of different width of MS plates. Automatic paint spraying mechanism is supplied along with the system, which sprays the paint on plate whenever any defect, is detected.
|